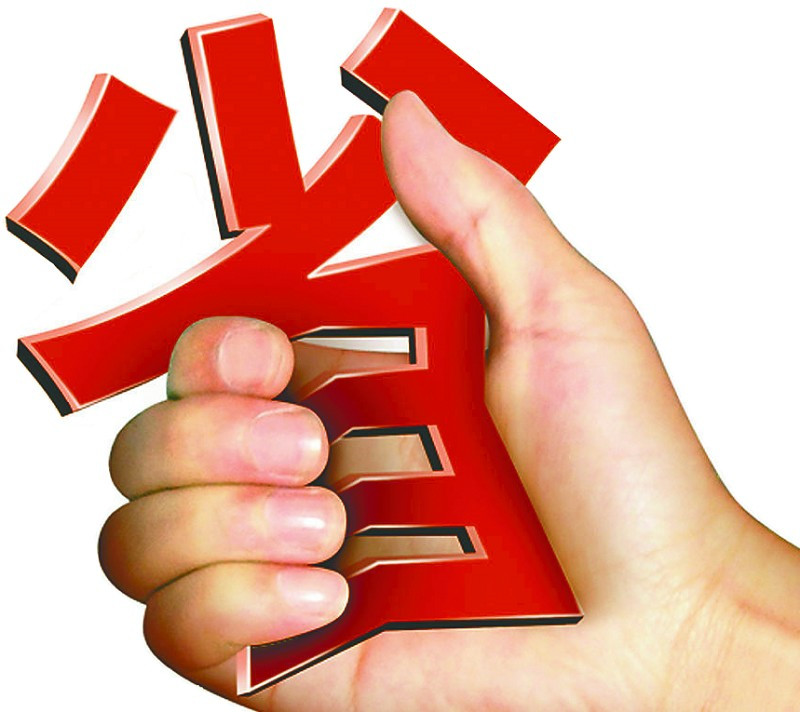
The core tip: aluminum profile defects are a factor in the waste, and a small defect on the aluminum profile will abandon the entire cut-to-cut aluminum profile. Due to the high added value of aluminum profiles, extrusion manufacturers should do their utmost to reduce defects in aluminum profiles.
1. Non-extrusion cycle time - Assume that the aluminum profile extruder has a production efficiency of 30 aluminum bars per hour, and each non-extrusion cycle saves 10 seconds, so you can increase the extrusion time by 2 hours per day for 2 hours. This means that more than 8% of the output is equivalent to a 8% reduction in conversion costs per kilogram of profile.
2. Downtime (running interruption) - The loss due to downtime is huge (the loss in our example is 48.00 yuan per minute), not to mention the lost capacity during the downtime because there is no output.
3. Extrusion speed - The production efficiency brought by the purchased high-tech aluminum profile mold should be carefully considered. If the purchased aluminum profile mold can achieve a faster extrusion speed than the extrusion mold itself, then a medium quantity order can make up for the extra cost of purchasing the mold. For example, suppose the normal cost is 2,860.00 yuan / hour, because the extra cost of purchasing high-tech molds is 10,000.00 yuan, as long as the extrusion speed increases by 50%, the basic production efficiency reaches 800 kg / hour, then an order of less than 10 tons It can make up for the extra cost of using expensive molds.
4. Using a porous mold, the extrusion speed can be increased by 200% (2-hole mold) or even 300% (3-hole mold), resulting in higher economic benefits.
One of the biggest benefits of using a modern aluminum profile tractor is that the tractor has the function of controlling the extruder to stop extrusion when the aluminum profile reaches the correct extrusion length. This is similar to the non-extrusion cycle, but since the extruded aluminum profile is just the required length, there is no waste of extrusion time. As a result, more costs can be saved, as the waste is reduced and the transport and recycling of the scraped waste is saved.
After the extrusion of the aluminum profile from the extruder, the most important goal is to increase the output and the shipment rate by reducing the waste, and send more products to the customer. Any scrap generated after extrusion will be very costly, so waste generation should be minimized in subsequent operations. To minimize waste, it is necessary to saw at the parking mark (the parking mark refers to the trace left on the profile during the non-extrusion cycle).
Only two techniques can be used to saw at the parking mark - ie, the flying saw cutting and the double length system. Flying saw cutting technology refers to sawing during extrusion. The use of the flying saw cutting technology makes it possible to cut the profile at the parking mark after the parking mark has come out of the extruder. The double length system means that after the second profile is extruded, the first and second profiles are cut during the non-extrusion cycle.
Both technologies have their own advantages. The double length system provides two air cycle times for the extrusion cycle, which is very beneficial for building alloys. However, the flying saw cutting system is less expensive (equipment cost and factory space cost) and allows one-bar multi-cut mode operation without stopping the extruder.
Both technologies can increase the yield by 1% to 2% (originally 1%-2% of the waste, which has now been converted to qualified products can be sent to customers). The conversion from waste to deliverables is a direct conversion of high value-added profiles, and the resulting economic benefits are enormous. If we calculate this growth as 1%, and take our aforementioned cost of RMB 2,860.00 per hour as an example, we can save more than RMB 1,000,000.00 in the 5-year recovery period compared to the tractor system that cannot be sawed at the parking mark. the cost of.
The aluminum profile moves on the extruder conveyor system - any movement on the extruder conveyor system can cause damage to the aluminium profile. For example, the modern transmission system uses a tractor to place the aluminum profile directly in line with the head of the stretching machine, so that there is no need to push and pull the aluminum profile on the belt table to make the profiled aluminum and the stretching machine jaws Align. Therefore, the possibility of the profile being scratched can be reduced.
Adjusting the gap between the aluminum profiles - the profiles are piled together and easily scratched each other. The modern conveyor system maintains the proper gap between the profile and the profile. In the process of arranging or collecting, it is not necessary to use a baffle to align the profiles.
Industrial aluminum profile mould
Manual operation by the operator - any time the operator touches the profile, the possibility of damage to the profile is increased. Profiles are susceptible to damage on the conveyor system, but are more susceptible to damage when the profiles are loaded into the aging bin and unloaded from the aging bin and packaged for shipment. In these aspects, it is necessary to strengthen the training of operators and raise the awareness of employees' cautious operation.
Maintenance of aluminum extrusion presses - The maintenance status of aluminum extrusion presses has a significant impact on the occurrence of aluminum profile defects. Whether the aluminum extrusion press is right or not, the condition of the ingot and the extrusion pad will affect the quality of the aluminum profile.
Residual air during extrusion - If air is introduced into the barrel during extrusion and then pressed against the pressure, the air is compressed to a small volume and the temperature is raised. The air heated by the compression will melt the surrounding aluminum alloy to generate bubbles in the aluminum profile, or the bubbles will explode after exiting the working belt of the mold, thereby forming pores on the surface of the aluminum profile. In either case, the aluminum profile will cause defects and lead to waste. There are three factors that may cause air to be carried in:
1. Residual gas caused by upsetting - the rod can only be loaded into the barrel if the diameter of the barrel is larger than the diameter of the rod. After applying pressure to the column rod in the barrel, the column rod is extended to the diameter of the barrel, and the carried air must be discharged. This air is released through the "exhaust cycle." The normal operation of the extrusion pad is very important for successful venting.
2. Gas residue caused by long rod hot shear - the shear surface generated by thermal shearing of the rod is impossible to be perfect and vertical. The simple long rod thermal shear causes severe distortion of the rod, resulting in an elliptical cross section and a large rounded corner of the cut end. Even with the most advanced long-bar hot shears, the corners of the sheared bars will always be rounded. This rounding easily causes air to remain when the rod is upset in the barrel.
The long stick hot saw can replace the long rod hot cut. The vertical rod surface can be sawed using a long rod hot saw. No deformation will bring air into it. However, some aluminum profile manufacturers do not want to use long rod hot saws because they produce aluminum chips when sawing. From the perspective of the economics of aluminum extrusion, it is very important that the aluminum chips produced by sawing do not take any extrusion time and cannot reduce the production efficiency of aluminum and aluminum profiles. These aluminum scraps are low-value scraps that do not increase the cost of any value-added processes. The only thing needed to handle these wastes is the cost of remelting.
If the long rod hot saw can increase the aluminum profile utilization by 0.5%, the cost of sawing aluminum scrap is lower than the value of the aluminum scrap. More than 90% of the installations installed in North America have turned their attention from long rod hot shears to long rod hot saws. There are also many users who have used long rod hot shears to upgrade their equipment to long rod hot saws, precisely because they have seen the fact that the use of long rod hot saws will greatly reduce aluminum defects.
3. Gas residue due to two-segmented splicing rods - since the surface of the two short studs is almost flat, there is little possibility of introducing air. The quality of the saw directly affects how much air is introduced between the two short studs. There is now a new technology to avoid the appearance of two spliced ​​rods. This is the rod rotating welding machine. Before cutting the rod of the required length, the rod rotating welding machine can weld the remaining rod of less than the set length to the next long rod, thereby eliminating the air brought in by the two splicing rods. The possibility.
Solid Contaminants - Like the air that is introduced during extrusion, defects caused by contamination can also destroy the entire length of the aluminum profile. There are two main sources of solid contaminants:
1. Warehousing - It is important to keep the factory clean. The place where the long rod is stored, the long rod heating equipment, the rod conveying equipment for feeding the aluminum extrusion machine, the aluminum extrusion machine and the aluminum extrusion machine are kept clean to avoid contamination of the aluminum profile. . Excessive lubrication is an important cause of contamination, and excessive lubrication can easily contaminate aluminum profiles. It is necessary to train operators how to perform reasonable but not excessive lubrication. Excessive lubrication is harmful to the process and is not beneficial.
2. Long rod hot shear pollution - many contaminants (such as oxides or dirt) on the surface of the long rod will enter the short rod when the long rod is cut. The shear of the hot shear has a characteristic that it will not remove any material. But long rod hot sawing can eliminate this source of pollution.
popular searches:  Aluminum art accessories    Luxury aluminum art villa door    Aluminum art stair railing   Aluminum art security window   Aluminum art fence    Aluminum art fence   Aluminum canopy
It is the nature of the baby to be lively and active. The baby spends most of the time playing and playing, so the dress should be loose and natural casual clothes. In addition, the baby's body is developing, wearing loose and casual clothes is conducive to the development of the body, but also gives people a comfortable and casual feeling.
Boys Down Jacket,Kid'S Down Coat,Down Puffer Jacket,Winter Puffer Jacket
Dongguan Yumuran Garment Co.Ltd , https://www.1movingkidsjacketes.com